Le défi de notre client c’était de réduire le coût d’un processus de fabrication, qui était déjà extrêmement optimisé, mais cela lui donnait la possibilité d’obtenir un nouveau contrat pour des références supplémentaires de la même famille de pièces, avec des volumes de fabrication plus importants et, partant, des revenus plus importants. Alors, il nous a contacté et nous a mis au défi d’améliorer ce processus.
Conditions initiales
- Processus hautement optimisé.
- Le client a déjà utilisé des bombes de 20 bars.
Installation du système haute pression 70 BAR
- La haute pression n’a été utilisée (initialement) que dans l’opération de forage : Drill Diam. 16 mm.
- Avec une pression de liquide de refroidissement de 70 bars, le temps de cycle a été réduit de 5s.
- La durée de vie du foret (carbure monobloc) a augmenté de plus de 70% (même avec des conditions de coupe élevées). La durée de vie du foret est passée de 750 pièces à plus de 1300 pièces.
- Dans l’attente de la mise en œuvre de la haute pression dans l’opération de coupure car le client devait acquérir les outils et les porte-outils appropriés.
Ce que le client a dit:
« J’étais plutôt sceptique quant à l’amélioration du temps de cycle avec une pression de liquide de refroidissement de 70 bars, mais une fois que SCS a installé son système SRHP et a exécuté la production pendant quelques heures, j’ai compris que l’amélioration était énorme et que le retour sur investissement n’était que de quelques mois. »
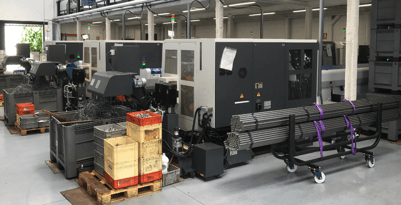
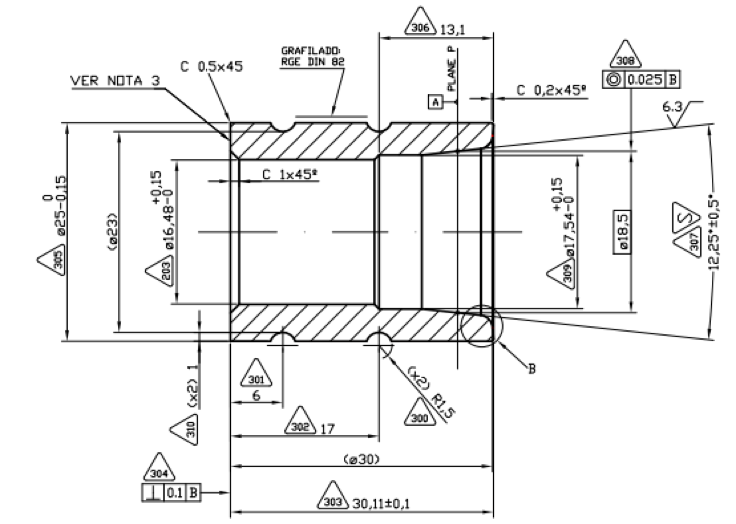
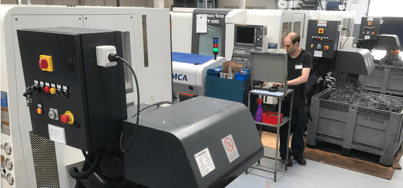