Conditions initiales
- Matériau à usiner: AISI-316l/EN14404.
- Partie utilisée: Barre pré-percée de 236 mm de diamètre extérieur et 150 mm de diamètre intérieur.
- Machine utilisée: Centre de tournage multiprocessus.
- Liquide de refroidissement utilisé: émulsion à 7%.
- Profondeur des conditions de coupe «ap» et avance par tour «fn»: fixée par le fabricant ; ap = 0,4 mm – fn = 0,2 mm/Rev).
- Vitesse de coupe optimale recommandée (Vc): 290 m/min.
- Durée de vie estimée de l’outil: 15 min avec une usure de l’outil de: 0,3 mm.
- Fin de vie de l’outil: Usure des arêtes de l’outil VB selon la norme ANSI/ASME b 94.55 M – 1985.
- Mesure d’usure: Machine à mesurer les outils Zoller Genius 3s
- Outil de coupe: Opérations de finition (CNMG12-04 -08-MF2015) pour acier inoxydable.
VARIABLES contrôlées
- Usure des bords de l’outil.
- Durée de la vie de l’outil.
- Taille de la puce.
Magnitudes utilisées
- Pressions de travail : 8 et 80 bars.
- Débit de fluide: 15 l/min
- Vitesses de coupe (Vc) : 250, 290, 330 et 360 m/min
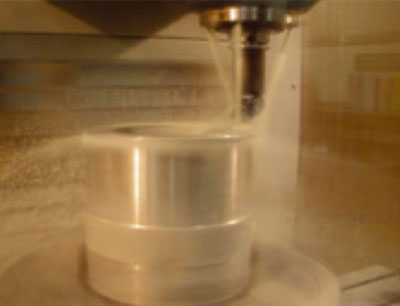
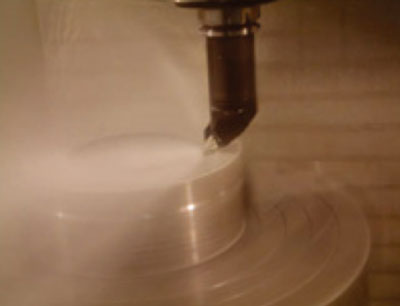
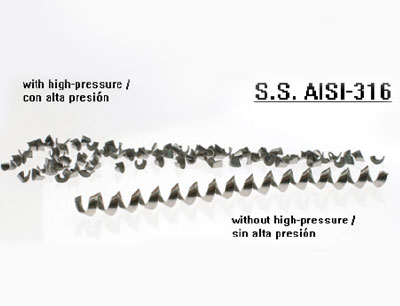
Résultats
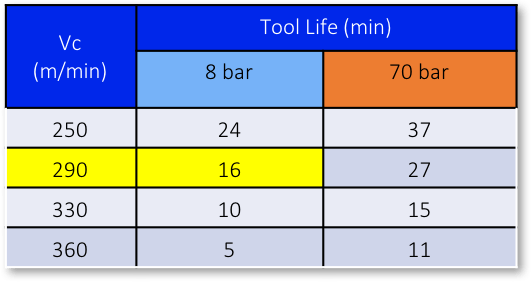
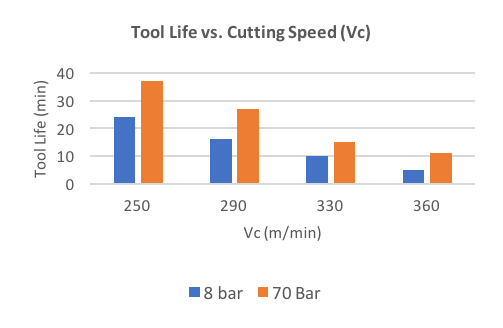
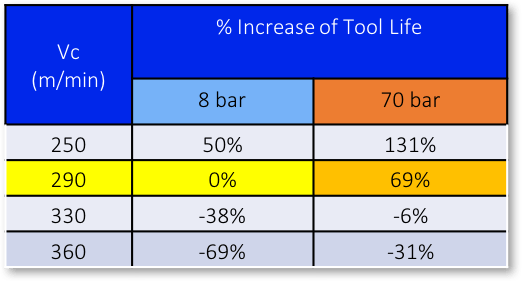
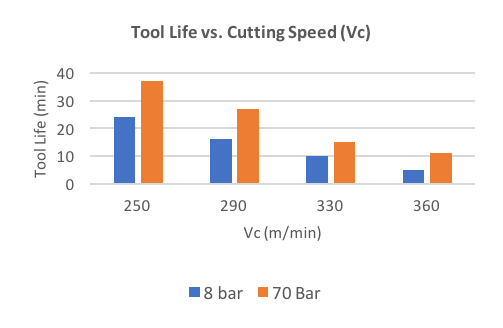
Conclusions (de 8 Bar à 80 Bar)
- L’utilisation de liquide de refroidissement à une pression de 80 bars augmente la durée de vie de l’outil d’env. 70%.
- L’augmentation de la vitesse de coupe permet d’augmenter la productivité. La durée de vie de l’outil est inversement proportionnelle à cette vitesse de coupe.
- L’effet du liquide de refroidissement à haute pression réduit la taille des copeaux de manière très significative, facilitant grandement l’évacuation de la coupe.
- L’utilisation de réfrigérant à haute pression permet un meilleur contrôle des copeaux et, dans les machines avec changeur d’outil, évite un bourrage éventuel de copeaux susceptible de réduire la fiabilité de la production sans personnel.
- L’investissement dans un système haute pression est rapidement amorti en raison de la réduction des coûts d’outils (durée de vie accrue), de conditions de coupe plus élevées avec la réduction conséquente du temps de cycle, d’un meilleur contrôle des copeaux qui permet une production plus robuste processus avec moins d’arrêts et en évitant les marques éventuelles sur la surface des pièces usinées.